The Problem
The company processes animal waste such as fish skins and other skins to extract gelatine. The plant had operated successfully for years using a combination of load reducing devices such as polyelectrolyte and balancing tanks. The feedstock to the production plant altered which meant the soluble BOD load increased massively and the plant struggled to cope.
The first indication of the problems with overloading was the air blowers were operating longer than the usual. The blowers were controlled by Dissolved Oxygen probe in the ASP, obviously the DO was not hitting the pre-set level of 1.5mg/L. As time went on, the blowers were permanently on, and the plant was discharging effluent greater than the 30mg/L consent limit.
Eventually, the discharge was black, and the ASP had gone anaerobic. The company were threatened with closure due to breaching the air and water discharge consents.
Waste Treatment Plant Details:
Flow per Day: 3.5mld
Inflow BOD: 10,000
Total KG BOD: 35,000kg/day
Design Flow: 3.5mld
Design Load: 20,000kg/day
BOD consent: 30mg/L
The Solution
Bio2pure set up a culture medium on site and started dosing with bacteria and Slow Release Oxygen compound to raise the DO levels.
The Result
Within 6 hours of starting the treatment the smell had disappeared and the ASP liquor had turned from black to a grey colour. After 48 hours treatment, the ASP liquor was a light brown, the DO in the ASP had risen to 1.5-2mg/L and the blowers were switching on and off.
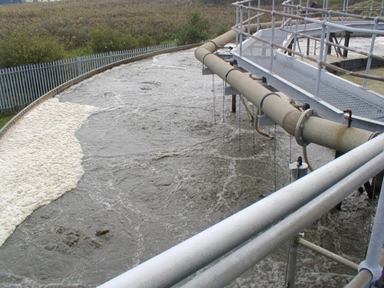
Activated Sludge Tank
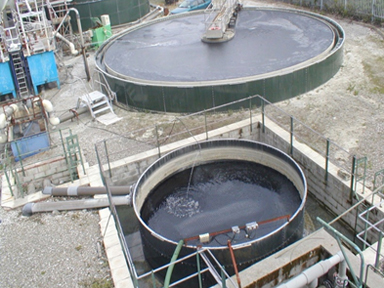
Secondary Settlement tank No 1 – Dosing Unit in the background